I promised to post an update on my Triumph (named Nigel) just about a month ago. I’ve made some great progress, and this time I remembered to take some pictures.
In the last update, I managed to get the car running, but only with the choke on. This seemed to point towards a vacuum leak, but I couldn’t find a strong one. Using the ol’ spray some carb cleaner all over the place method, I learned the spacers between the carburetors and intake manifold weren’t making an airtight seal. I ordered new spacers and gaskets, and that actually made a big difference. Along the way I also removed the EGR system, disconnected the vacuum retard on the distributor and the bypass valves on the carburetors. I may reinstate the bypass valves after some driving.
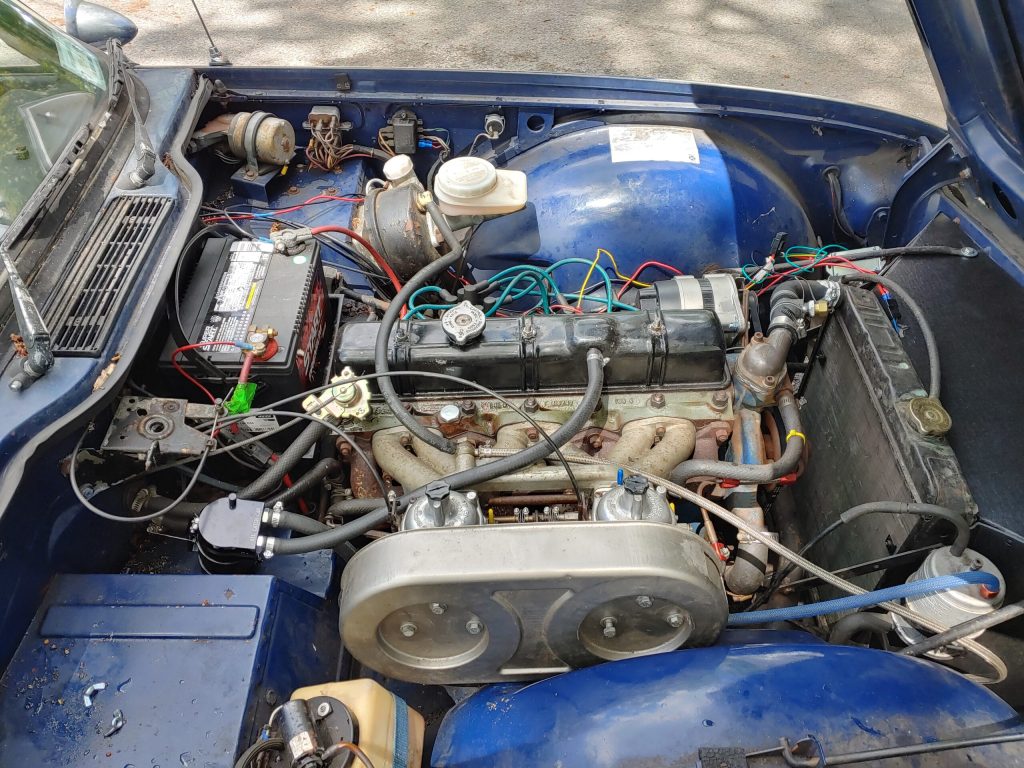
At the same time, I discovered the vent port on the rocker cover was spewing smoke into the carburetors, upsetting the airflow and causing difficulty with keeping the engine running. I rerouted the engine fumes into an oil catch can, but I may try to put this system back to stock in the future. The catch can doesn’t catch everything, and smoke still comes out of it. I think this is probably a sign that the piston rings could use replacement, but we’ll see how it goes. I’d like to kick that can as far down the road as I can. I’ve read that filling the engine oil to the top mark on the dipstick may in fact overfill the engine, so I’m going to try putting somewhat less oil in when I change it.
I also advanced the ignition timing quite a bit, enough to be off the scale on the crank pulley, and that made the biggest difference in the engine’s ability to run normally. Whether the timing is actually about 26° BTDC, I don’t know. The crank pulley may not be correct anymore. I’m hoping the timing works on the road, because the engine has never run this well or been this easy to start before. Reports on the TR6 forums suggest that this timing will probably be fine, but it varies car to car.
Moving to the other side of the engine, you can see the new wiring for the electric fan.
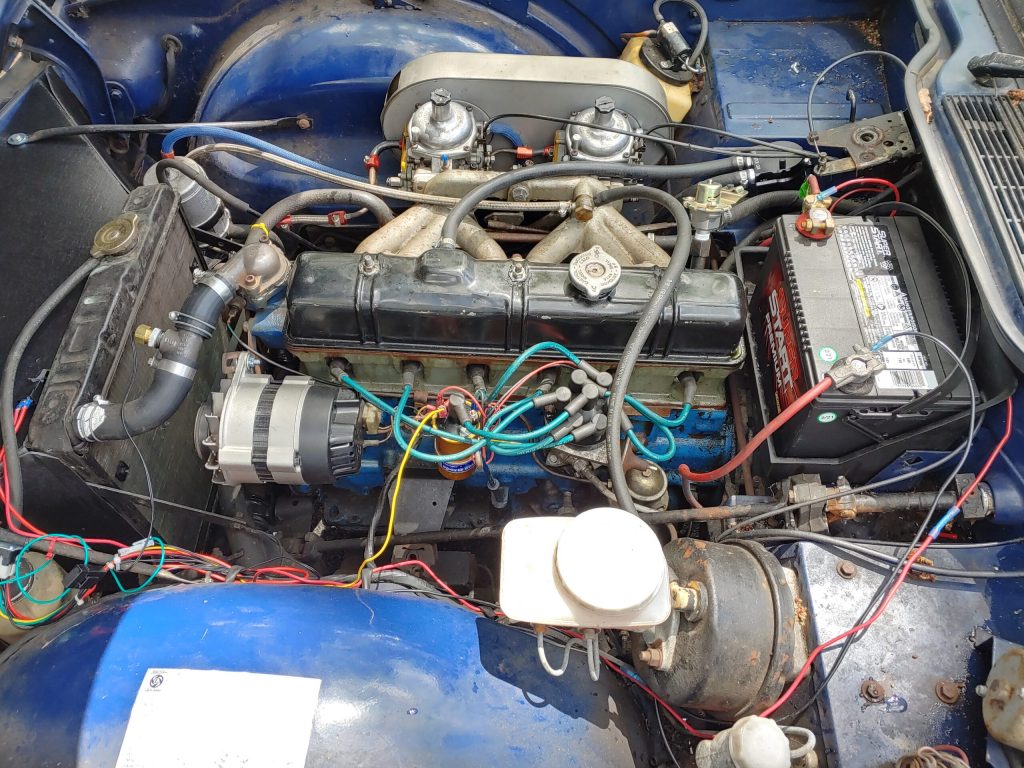
The bundle of wires below the radiator are for the fan controller, which works wonderfully. Part (or maybe all) of the reason it wasn’t working was because I had it wired wrong. I may not have needed the new temperature sensor, but it’s a lot more elegant than shoving a probe into the radiator fins. The only problem with it is the fan uses a lot of electrical power. With the engine idling, there’s barely enough power to run the ignition system and the fan, so the engine comes close to stalling. I just had the original alternator (a 40 amp unit I think) rebuilt, so I don’t want to replace it now, but I might next season. There are plenty of higher output options for the TR6.
Today I decided I’d see if a polish and wax would wake up the paint at all. I had mixed results, but no parts are worse than before.
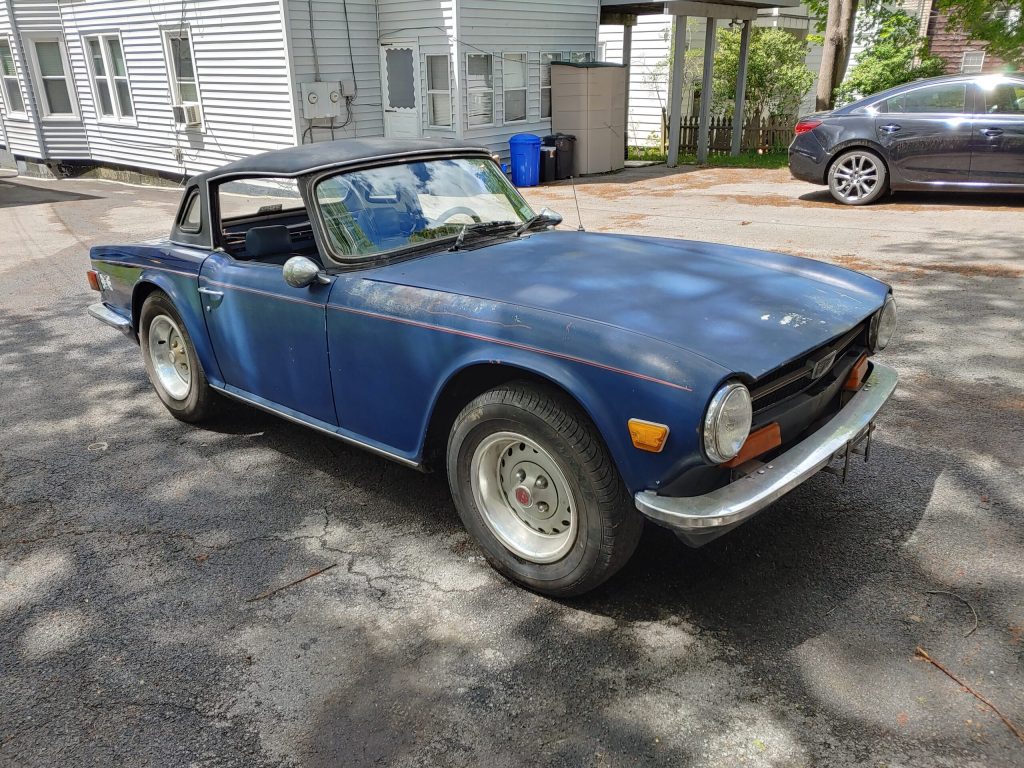
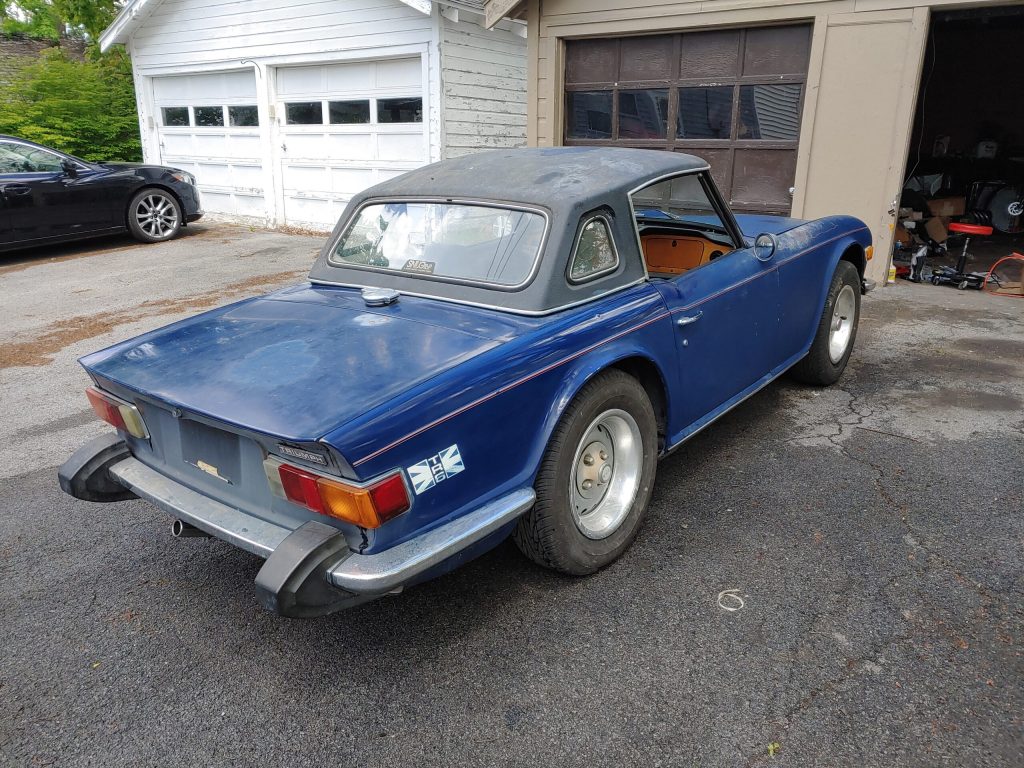
The right front portion and the hood is slightly better, but not great. The right rear is actually not terrible. The trunk has a couple spots I need to grind down and hit with primer soon.
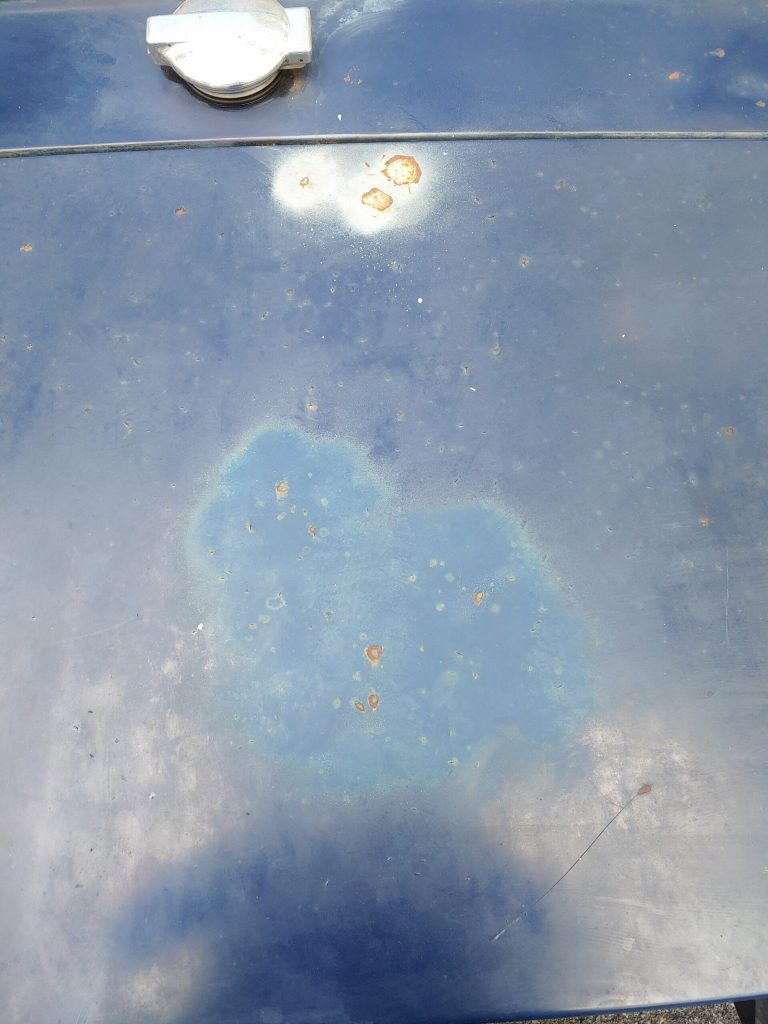
The vertical surfaces of the left side however, came back pretty nicely.
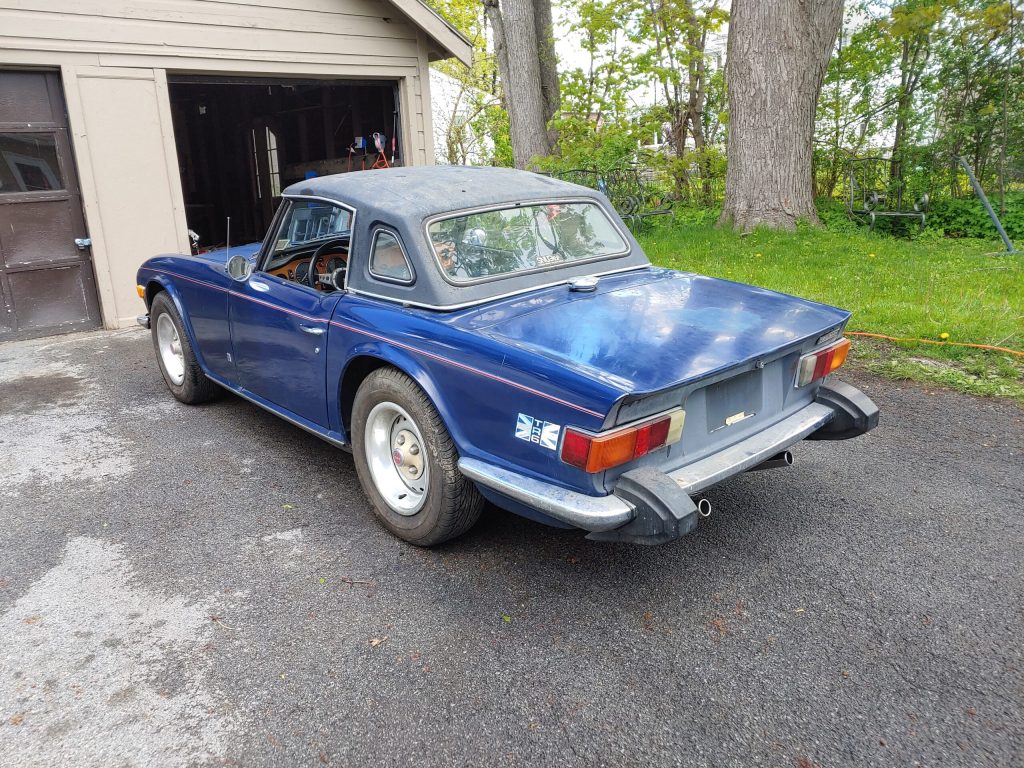
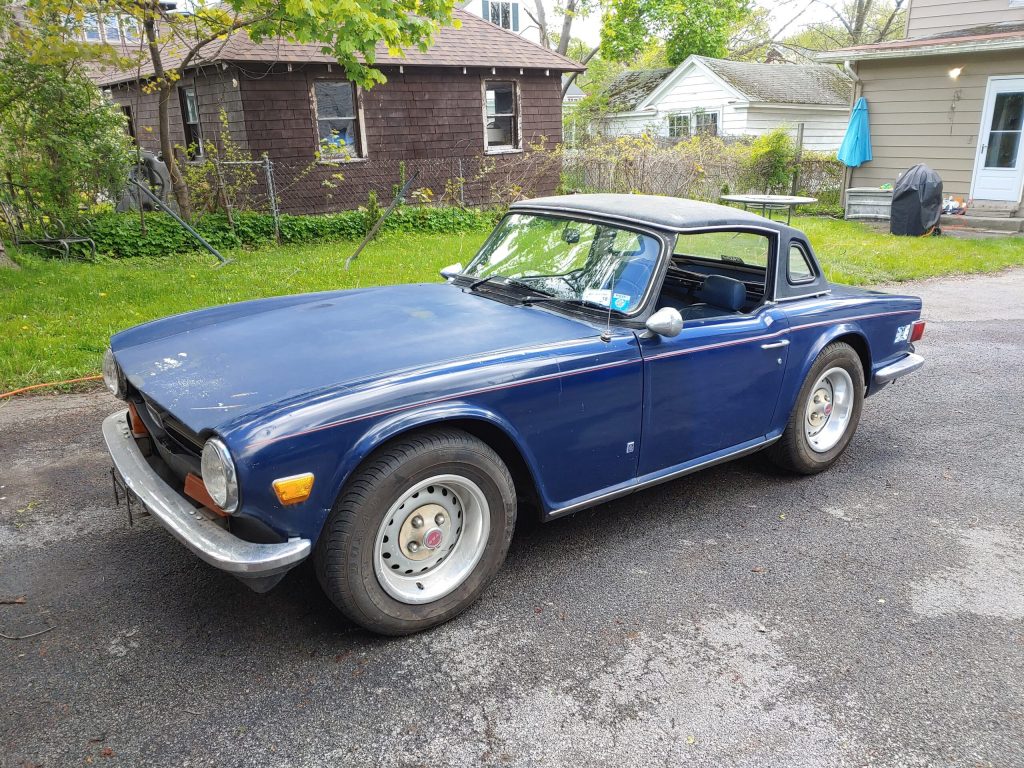
Just like the engine could probably use a rebuild, the body needs a repaint. A good paint job will be out of my budget for the foreseeable future though. Plus I don’t know what color I’d paint it.
The interior isn’t in amazing shape either, but it stays put together. I need to get carpet some day and replace the trim near the center control knobs.
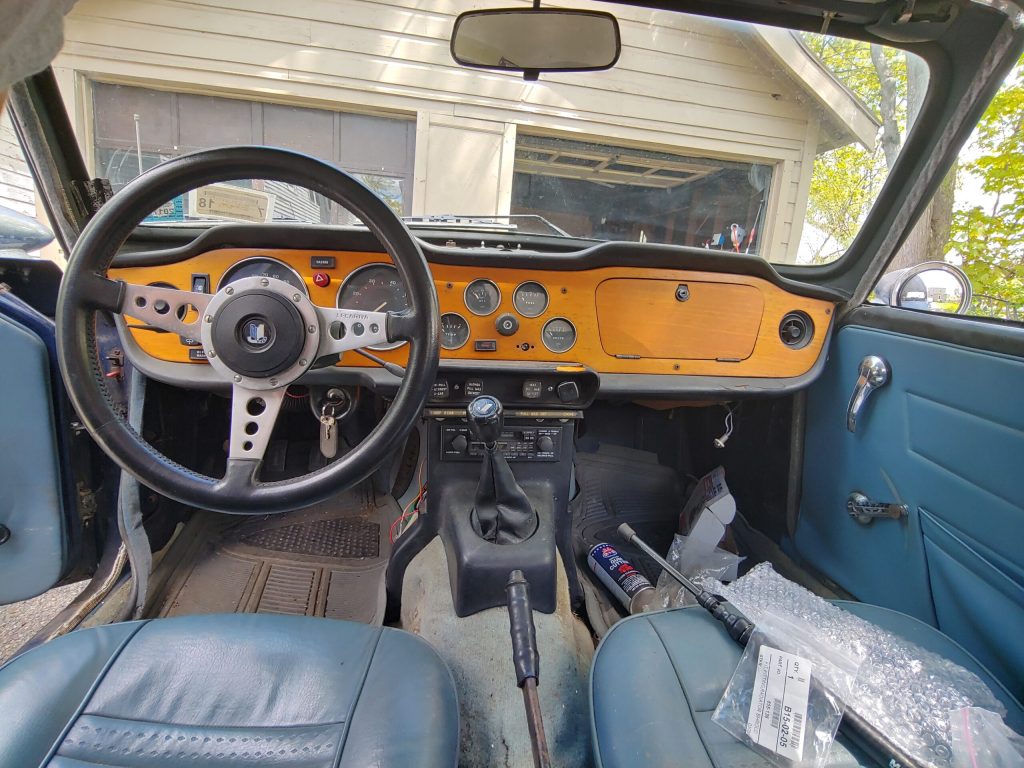
The car just needs a tail light socket and it’ll be ready for inspection. That and an a few other parts should be in tomorrow. I have new engine mounts already that need to be installed in the next couple weeks. My latest order includes new front shocks and wheel bearings, plus parts to help replace the half shaft universal joints. I’ve had the joints themselves for a while now. I need to replace the rear shocks and springs too (especially with the new exhaust, the mufflers hang really low), but they’ll have to wait a little while.